Geopolitical factors, import and export uncertainty, and inflationary pressures are influencing the manufacturing sector and the decisions it faces regarding supply chains. Dependence on external supply chains may present various risks and will require careful risk management, business continuity, and resilience planning.
Taking the Pulse of The Sector
In the most recent National Center for the Middle Market (NCMM)/Chubb survey of CEOs and financial executives of middle market companies – fielded in December 2024 –, nearly one-third (31%) of manufacturers said they were impacted by supply chain disruptions/constraints in the past six months. When asked about the challenges they face around supply chains, respondents ticked off a list of difficulties including raw material shortages, impacts on imports and exports, increased transportation costs due to congestion and driver shortages, and dependency on global suppliers. Notably, some 30% of survey respondents report sourcing raw materials from China, 23% from Mexico (NCMM). Supply chains ranked third among these executives’ top risk challenges, behind inflation/recession and talent shortages/workforce retention. (Read more about risks for midsize businesses in this WSJ article)
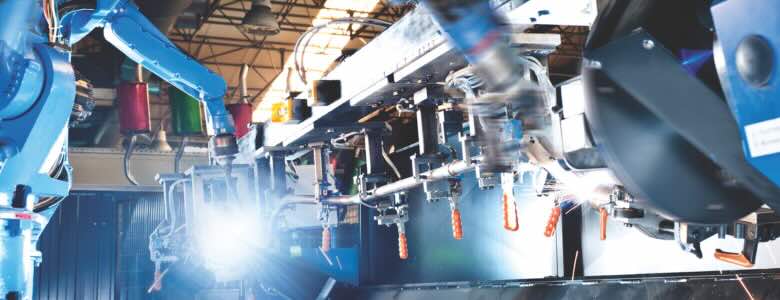
The increased frequency and severity of climate change, driven by severe weather events, is a major contributor to supply chain disruptions. A full 58% of manufacturers pointed to supply chain disruptions as their top concern associated with climate change. Geopolitical upheavals, cybersecurity incidents, and labor strikes can also tilt supply chains off balance, while economic strains increase the chance of vendor bankruptcy or insolvency.
As manufacturers move into new territories – and some 49% said they are extremely or very likely to expand internationally in the next 12 months – it adds additional complexities. Building codes, and in particular fire protections, are often not as stringent as those at home. Natural catastrophe risks and power and transportation infrastructure differ significantly throughout the world. Laws governing insurance and business practices vary. All of this must be navigated whether a company is establishing its own operations or contracting with supplier or distributors abroad.
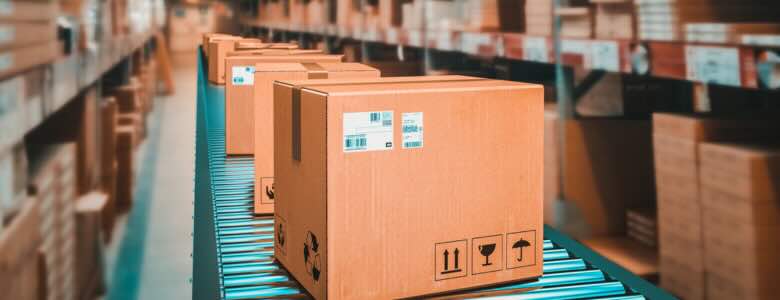
A Roadmap for Resilience
When it comes to minimizing supply chain risks and disruptions, factors like geopolitical upheaval and natural catastrophes are not within a company’s control. Several factors, however, are in an executive’s control, starting with the creation of a formal, written business continuity plan (BCP) – a procedural document that lays out courses of action to minimize operational downtime should a disaster or disruption strike. When operations depend on external suppliers or vendors, business continuity strategies must carefully assess and address supply chain vulnerabilities. The following foundational steps can help:
- Involving supply chain leadership. Supply chain managers should be part of a company’s cross-functional BCP team, alongside experts from finance, insurance, strategy, and operations. Their insight is critical to identify company-specific risks, interconnections and potential redundancies.
- Identifying critical suppliers and supporting partners. Determine which vendors are essential to your business, especially those providing goods or services that are difficult to source elsewhere. Don’t stop at direct suppliers — include second- and third-tier vendors, contract manufacturers, warehouses, distribution hubs, and logistics providers to get a full picture of your supply chain network.
- Assessing supplier-specific risk. Each vendor has its own vulnerabilities — from geographic risks to facility readiness. Suppliers in high-risk areas (e.g., earthquake or hurricane zones or locales with building codes that may leave them exposed) should be evaluated for structural resilience and emergency planning. The interconnectivity of a vendor’s systems – and the cyber security protecting its systems – should be understood. Questionnaires, checklists, and site visits can help companies assess individual suppliers and prepare accordingly.
- Holding vendors to BCP standards. Vet suppliers carefully for resilience and reliability. Understand their business continuity planning and spell out contractual expectations, including insurance and communication protocols in the event of a disruption. services are available to help manage documentation, such as insurance certificates, and to track compliance.
- Preparing to minimize disruptions. Identify and pre-qualify backup suppliers and be ready to pivot to them to reduce downtime if a key vendor goes offline.
Proper preparation is not just a matter of maintaining business operations. In a vastly interconnected marketplace, it can be a decisive competitive advantage. Middle market companies may find value in the insights of global insurers like Chubb when working to enhance supply chain resilience. Insurers can provide coverage for supply chain disruptions and related business interruption losses.
For more insights, download Chubb’s survey: Middle Market Indicator: Performance, Outlook and Dynamics.
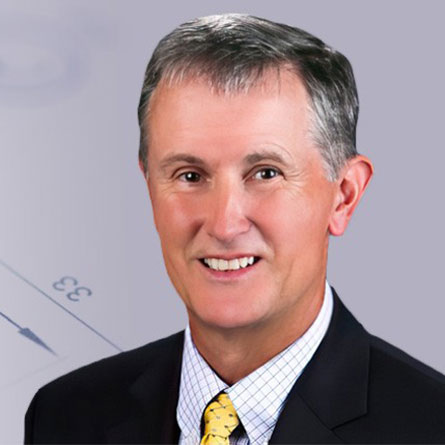
Michael Williams
EVP, Chubb Manufacturing Industry Practice Leader
Chubb is the marketing name used to refer to subsidiaries of Chubb Limited providing insurance and related services. For a list of these subsidiaries, please visit our website at www.chubb.com. Insurance provided by ACE American Insurance Company and its U.S. based Chubb underwriting company affiliates. All products may not be available in all states. This material contains product summaries only. Coverage is subject to the language of the policies as actually issued. Surplus lines insurance sold only through licensed surplus lines producers. The material presented herein is advisory in nature and is offered as a resource to be used together with your professional insurance advisors in maintaining a loss prevention program. It is not intended as a substitute for legal, insurance, or other professional advice, but rather is presented for general information only. You should consult knowledgeable legal counsel or other knowledgeable experts as to any legal or technical questions you may have. Chubb, 202 Hall's Mill Road, Whitehouse Station, NJ 08889-1600.