Business growth, particularly for middle market firms that focus on manufacturing, often translates into facility expansion. As your business grows, your factories can only accommodate so much additional business through more supply lines and expanded hours, and eventually, you need to increase physical capacity.
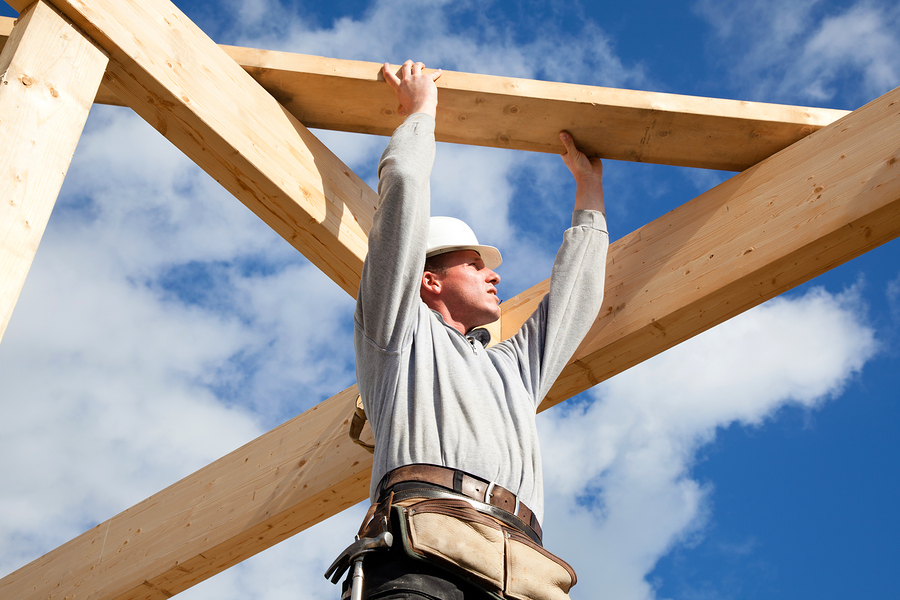
Assuming that you've maximized the possibilities of an existing facility, expansion inherently brings up the question of where to move and whether to buy or rent in the potential new location. There is no simple, easy answer here, given the numerous variations involved, but there are at least 12 questions you should consider to make a prudent decision:
- Do you need to move? If you can manage expansion within your existing operations, it might make sense to stay where you are. Any move will be disruptive, so be sure you really need it. Particularly if an uptick in business is an unusual or periodic spike, consider if there any other alternatives such as running an additional shift, adding a line in an existing location or outsourcing overflow to a contract manufacturer.
- How does location fit into your overall strategy? Proximity to vendors, distribution points, large customers, expertise, natural resources, transportation options or other factors may be related to location. That could restrict choices if a suitable location is not available.
- How close are important resources? Even if location is not a primary consideration, you do have to consider whether distribution partners, suppliers, large customers and other important resources are close enough or if distance could have significant business implications. For example, a rental facility placed near transportation might cut logistics expenses enough to more than compensate for other expenses that may be higher, such as power or local taxes.
- Are there tax benefits of buying versus renting? See whether a rental or purchased location might open the door to incentives, tax credits or other financial benefits. This could be true on a local, state or federal level, so do your research.
- Are you moving a single operation or multiple? The more business growth you see, the more locations you may already have and the more complex the calculations. Rather than renting or buying an additional space, would it make sense to combine multiple operations and collapse them into one facility?
- What are your options for available locations? Will a new location have the capabilities you need? Or will you face restrictions from existing zoning and building code requirements, or from what an owner is willing to allow on a rented property?
- Does the location need modifications? Related to the previous point, consider whether a given location will need significant changes. In a rented facility, can you make permanent modifications? Would modification of an existing structure, whether rented or purchased, have benefits that offset building a custom facility?
- What is the role of technology? Technology plays a big part in manufacturing, and new methods can offer significant incentives for increased profitability to middle market companies. Be sure that a space can be changed to accommodate any worthwhile new technologies. If the location in question is older and you're considering renting, there might be communications or power requirements that would require too great of an overhaul to be cost-effective.
- What is the value you could gain from a custom build-out? Depending on the states of existing facilities and current technical capabilities, balance an increase in productivity and cost-effectiveness against the price of building a new factory or office on either purchased or leased property.
- Are there adequate prospects for local staffing? Whatever location you choose, you want an available workforce that is appropriately experienced and trained for your operations. If the choice between facilities means putting your operations beyond a reasonable commuting distance from prospective employees, it could present a problem.
- What research and training at local schools could help? Universities and technical high schools can be sources of labor and also of collaboration with researchers or teachers who can help improve operations. A property, whether leased or purchased, that offers ready access to a local school may offer significant soft benefits.
- How long do you envision operating in the new location? Longevity can make an enormous difference in whether a purchase or lease makes the most financial sense. In addition to straight cost comparisons, consider tax issues such as depreciation time lines. There may be a point when it becomes more economical to own rather than rent. At the same time, a longer-term lease can give you more negotiation strength to push down annual rental costs.
Are there any other important questions to consider when thinking about expanding manufacturing operations? Let us know what you think by commenting below.
Erik Sherman is an NCMM contributor and author whose work has appeared in such publications as The Wall Street Journal, The New York Times Magazine, Newsweek, the Financial Times, Chief Executive, Inc. and Fortune. He also blogs for CBS MoneyWatch. Sherman has extensive experience in corporate communications consulting and is the author or co-author of 10 books. Follow him on Twitter.